Dynamic Foundation Engeeniering
We are the leader in Grouting machinery repairs
Our specialty is to address the entire project, from technical analysis to Grouting.
We have carried out more than 4,000 projects for all types of machinery, both dynamic and static, for clients in the petrochemical, steel, fertilizers sectors, and other industrial complexes.
For this, Apoltec has all the resources and training necessary to quickly start working in any installation (in confined spaces, work at height, chemical complexes, etc.)
In case an existing machine shows a lack of stability foundation due to a degradation of its grout by oil and vibration, Apoltec provides a solution to substitute the existing grout without removing the equipment, saving time and complications for the end-user.
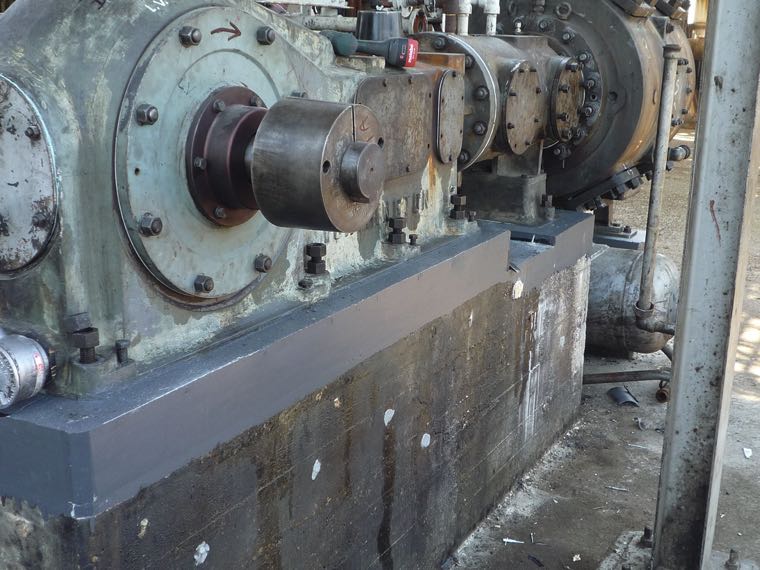
Equipment foundation repair:
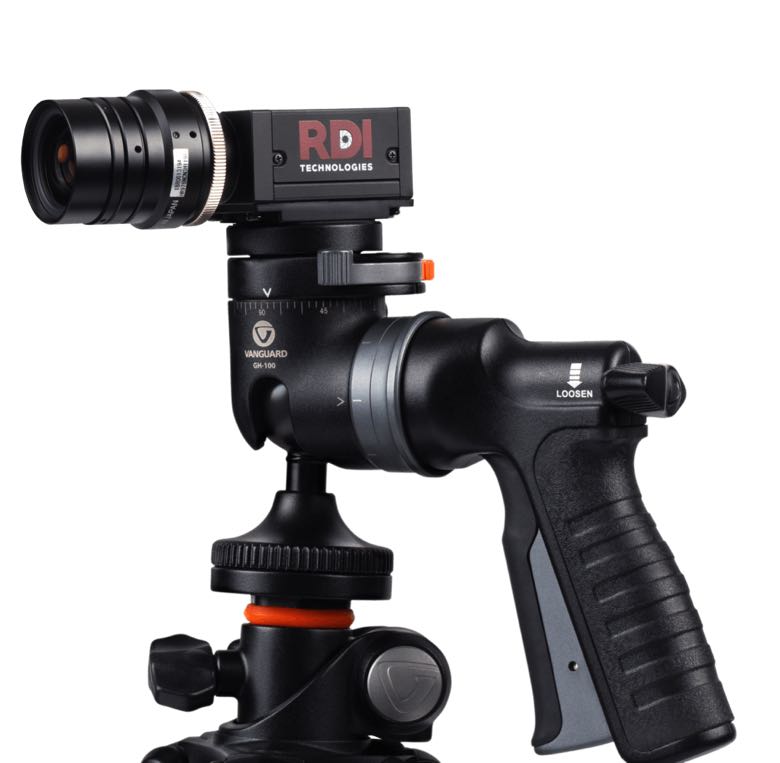
1. Technical Analysis And Inspectioncabezado
Physical visit + Analysis for the preparation of the technical project and the security plan.
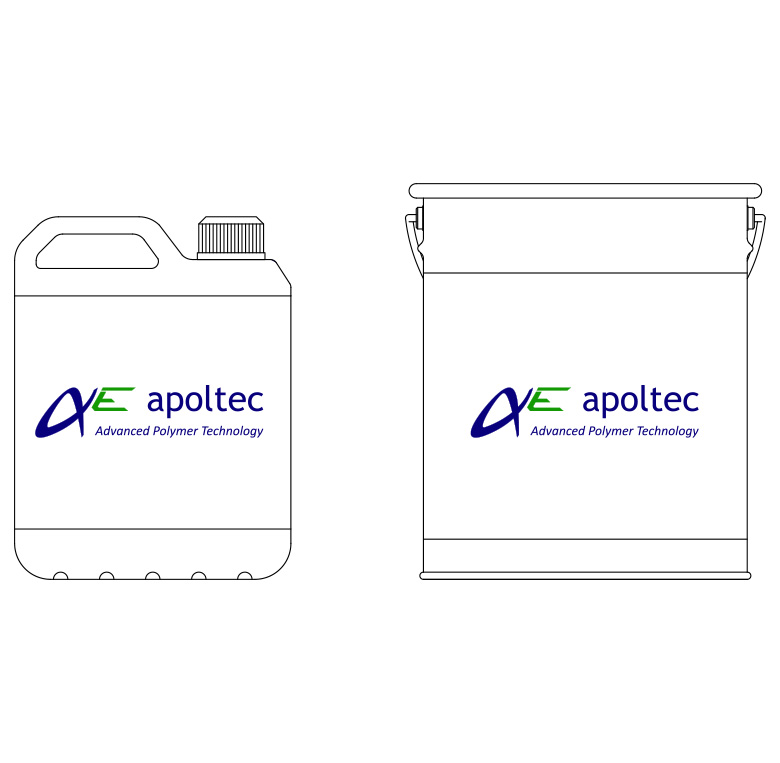
2. Selection Of The Suitable Apoltec
Products to achieve the project depending on climatic, chemical factors, support needs, one or the other will be chosen.
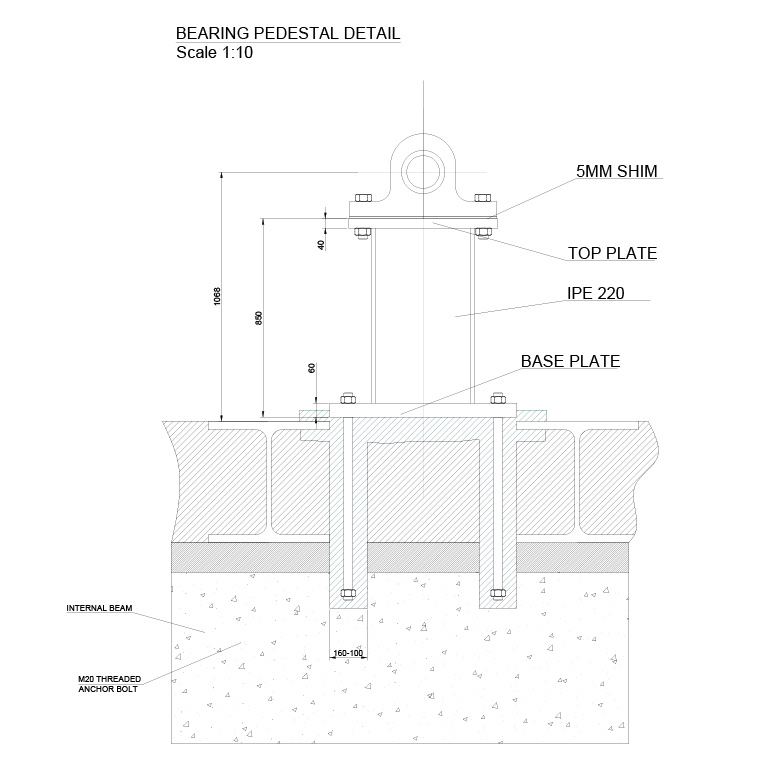
3. Design And Manufacture Of Frames To Support The Machine If Necessary
Our engineering team is capable to design and manufacture the frames if it is needed.
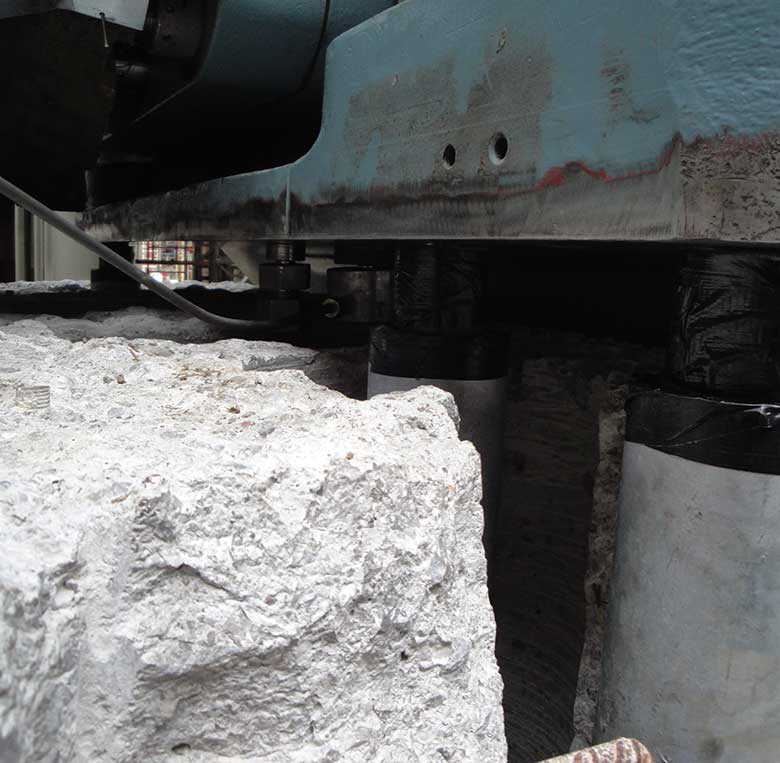
4. Demolition Equipment Foundation
Demolition of the surface of the original base and re-foundation of the unrecoverable points.
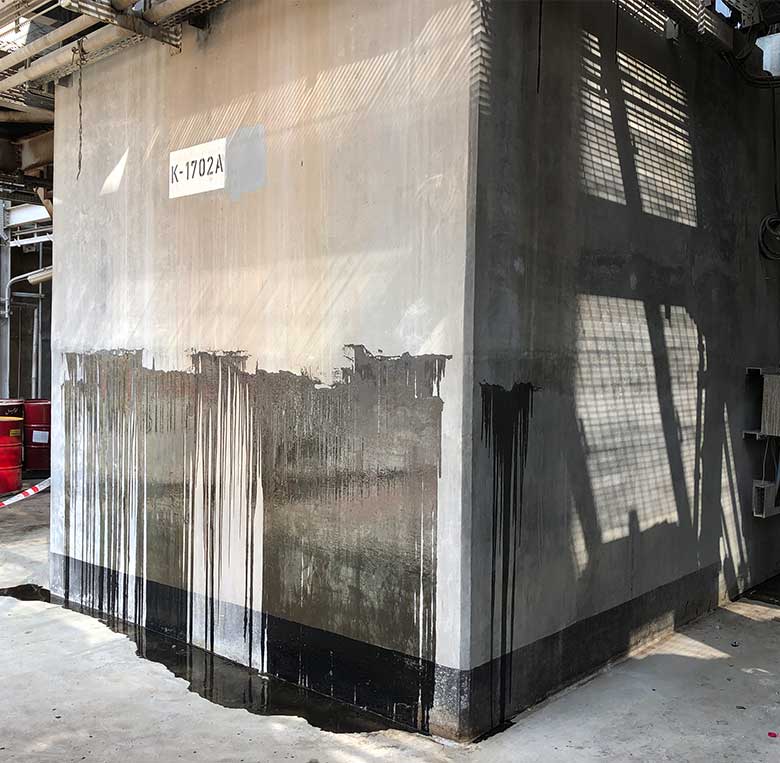
5. Epoxy Injection And Crack Repairs
High pressure injection of our Apoltec 370 resin for the consolidation of the bench and the extraction of filtered residues. This resin is specific for adhesion on oil contaminated surfaces, such as cracks or separations of rotating machinery, it has been extensively tested in foundations of diesel engines, reciprocating compressors, mills, presses, etc.
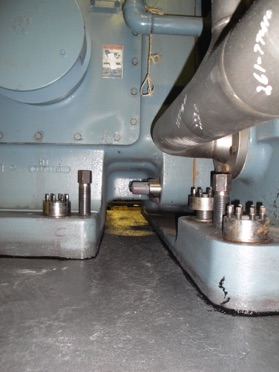
6. Anchor Bolt Removal And Replacement
Apoltec can provide a wide range of solutions in case of an anchor bolt break. We can provide the design and realize the installation of all sizes of anchor bolts.
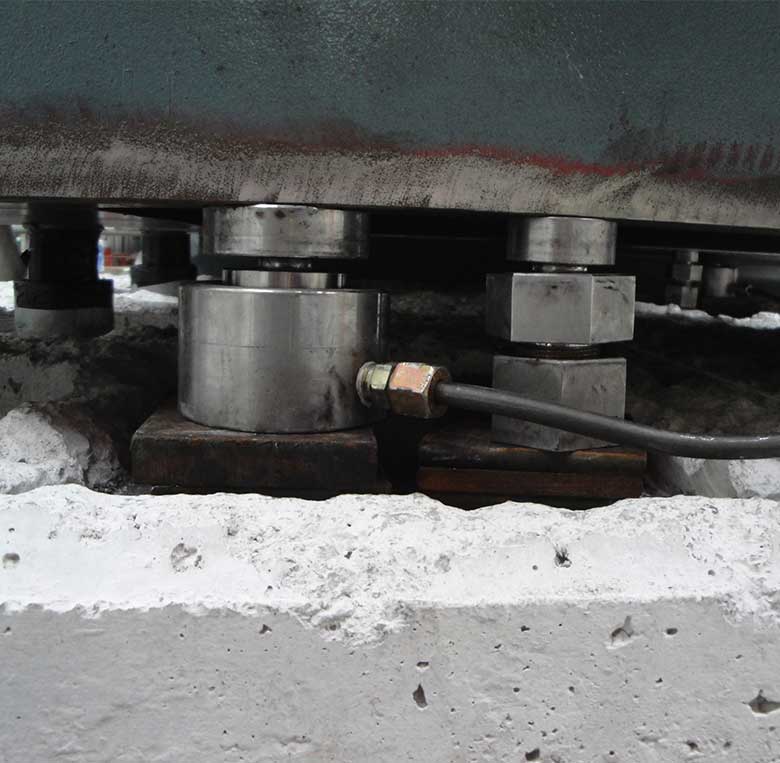
7. Lift With Our Hypads
To avoid “hardspot”, Apoltec can provide hydraulic pads able to sustain any machinery and ease their leveling.
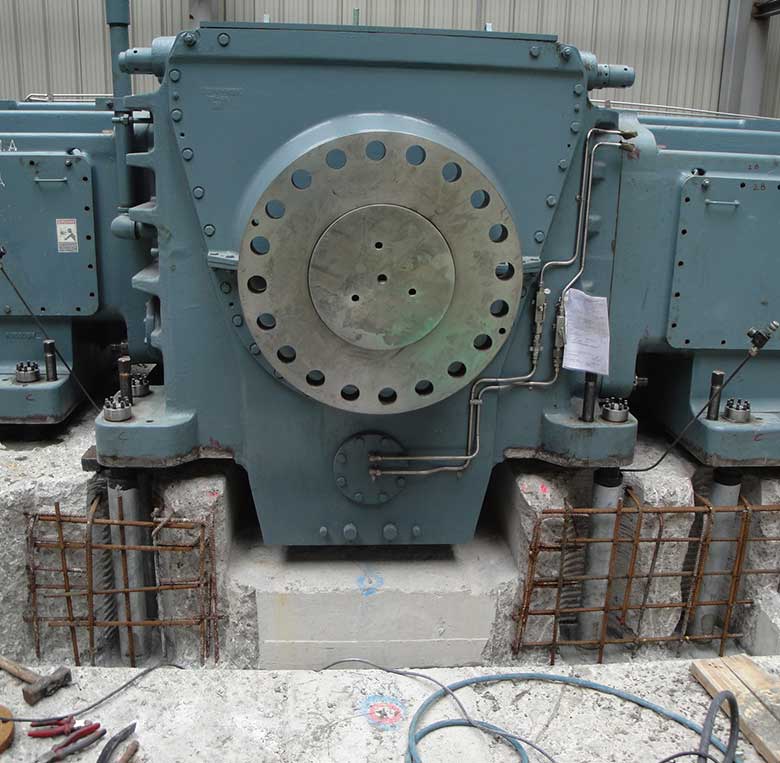
8. Machine Leveling
Apoltec facilitates and helps to level the machinery if necessary. We have dial gauges and meters to analyze and correct possible deviations of the machine with respect to the alignment point.
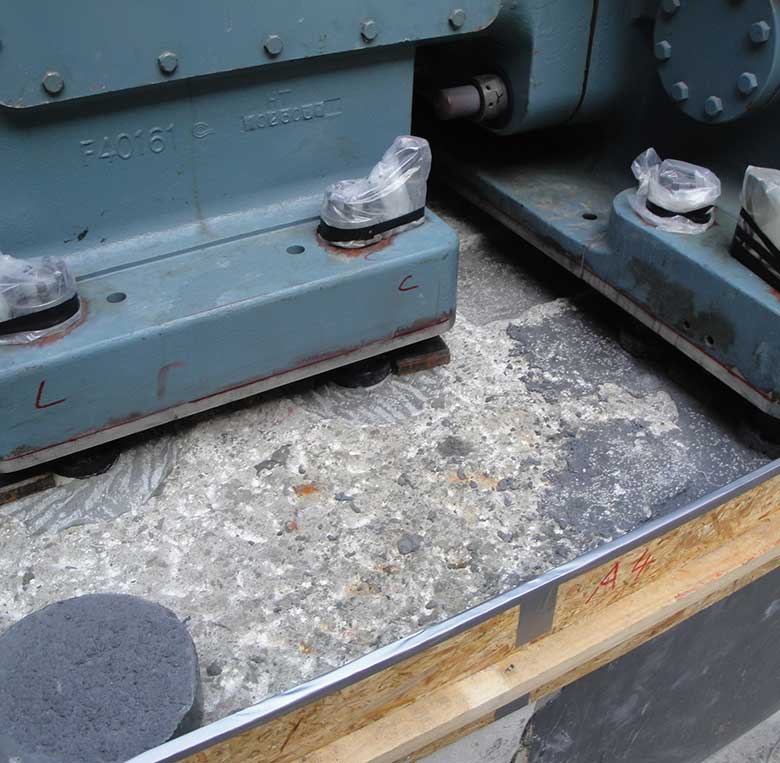
9. Formwork
We design and manufacture the formwork according to the location and needs of the grouting.
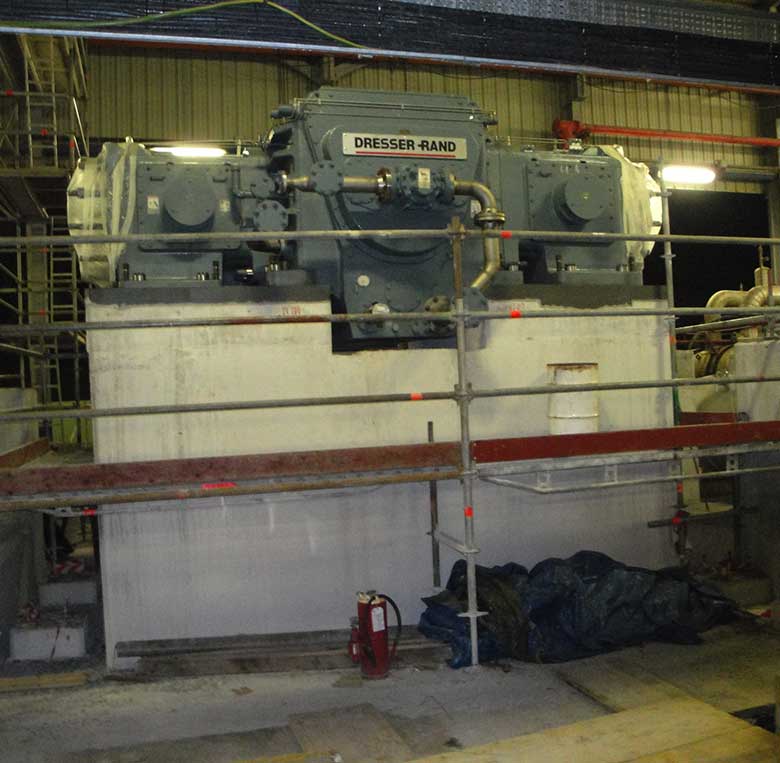
10. Machine Grouting
We have more than 20 years grouting heavy machinery. Depending on the place, frame, and the footprint of the equipment we will choose the best way to proceed.
FAQ
1. Dampening Sytem
Dynamic function of a dampening system consists of efficiently absorbing and attenuating residual mechanical energy exerted by the machine and its transference to the subsoil as natural spring.
A standard dampening system comprehends:
Frame, which is consider the highest rigid structure being part of the machine case or not (mounting frame, skid, sole plates, rails, …). It’s hold down to the foundation thru the anchoring system.
Anchoring system, performs as device for displacement restrain and is critical for modifying the tensional state of underlying materials in order to better resist fatigue.
Grout, is a layer that connects machine to the main foundation inertia block and has an essential dampening and inertia restrain duty.
Foundation, in the way of mat or slab, base rafts, columns, pillars, plinths, inertia blocks, and so on, lowers gravity centre, increases and adds inertia mass to the machine, dampers vibrations, and compress under pressure subsoil materials.
Subsoil, as a natural spring for energy dissipation. It is tuned on phase by all elements above.
A dampening system is submitted to continuous solicitations in the form of mechanical, thermal and chemical stress. Progressive degradation means loosening dampening efficiency in both ways, lack of energy absorption and transference.
This condition affects immediately the equipment reliability increasing tearing & wearing of machine parts (structural, as crankcases, frames, anchors & fasteners, packing,…, and dynamic, as crankshafts, bearings, rods, plungers,…). Firstly, recurrent breakdown (pieces wearing, gaps, heating, noise, misalignment,…) is more frequent and it could advance catastrophic failure.
An optimal dampening system is always related to economics: extend safely and reliable equipment production life, it reduces non scheduled shutdowns, it reduces energy consumption and it contributes to safety operation.
2. Dynamic Stability
An integral stationary machinery re-installation consists in the entire reconditioning of the dampening system, getting back –even improving them- the design mechanical parameters in order to assure the equipment dynamic stability consistently.
Dynamic stability means mechanical reliability: the equipment has the ability to transmit its stresses to the soil all along through an intimately and ideally rigid connection with a mass (energy absorption) system.
Preventive maintenance has to consider checking regularly the dampening system and installation condition in order to detect eventual future failings.
Summarizing these are the positive consequences of achieving dynamic stability:
• ∆↑Reliability → savings in operational costs and due to non-scheduled shutdowns
• ∆↑ Operating life → savings in running costs
• ∆↓ INDIRECT energy consumption → increasing mechanical output
• ∆↑ Safety operation → reducing catastrophic failure likelihood
3. Know How
A successful integral dampening system reconditioning, or complete equipment re-installation consists on consider it as a monolithic, uniform and continuous mass intimately connected to the machine. At the same time, all this mass tunes on phase the natural spring (subsoil) which has its particular mechanical features and elastic & damper parameters.
There are several symptoms revealing an incipient dampening system fatigue, for instance:
- Cracks induced by thermal and mechanical stress.
- Oil penetration that counteracts friction response against lateral movement or detaches grout from machine footprint, anchor bolts or foundation.
- Corrosion of peripheral rebar, anchor bolts or bed frame surfaces that affects alignment and vibration isolation response.
- Cold or construction joints separation that discontinues foundations as a continuous mass behaving as undersized dampener.
- Shear stress on anchor bolts or loss of stretching and torque.
- Air gaps underneath mounting frames where oil can be drawn in or to allow resonance
- Subsoil differential settlement which may increase rocking movement.
All these, an others symptoms, alert us upon pathological processes affecting efficient task of dampening system. For instance, oil penetration lubricates surfaces, limiting friction and adhesion. Loss of “superficial integrity” of grouts is particularly critical since wearing away the intimate contact ends in anchor bolts tension loss that increases vibration and displacements and gets through coupling misalignment or crankshaft web deflection.
Our know-how lies on conceiving dampening system as a whole body which always has to keep its integrity and intimately coupled to the machine. Because it suffers mechanical, thermal and chemical stress, restoring these conditions must, at some stage, be strongly recommended in order to guarantee mechanical reliability. Our expert involvement will head to this target developing a specific technical repair procedure.
Apoltec, as applied ENGINEERING will carry out a complete technical survey to provide a turn-key solution.
→ detect symptoms
→ identify causes
→ design solutions
→ elaborate a technical project
→ develop a specific repair process and,
→ job execution
→ Regular inspections
Within maintenance shutdown or production demanding, pursuing to minimize idle time (equipment out of service) mostly of jobs can be executed by keeping equipment in position (machine on site) and using higher quality materials, devices & equipment.
4. Mechanical Adjustments
A proper machinery installation implies the thorough checking and adjustment of the equipment bodies leveling and elevation, coupling alignment and crankshaft web deflections. According to or under supervision of the manufacturer or mechanical contractor, the precise position of the equipment is achieved.
The precision displacements are carried on by means of adjustable devices: hydraulics, mechanics or a combination.
Any case, there is critical –specially on reciprocating and turbo machinery- to avoid the presence of “hot spots” or differential pressure points which, through them, the stress energy (mainly in the form of mechanical vibrations) is canalized. The stresses concentrate on such points and are not evenly distributed all along the bearing surface. In such conditions, the grout –as the interface between the bed frame and the concrete foundation- may suffer excess of solicitations (loosening its dynamic-mechanical features), also the anchor bolts, and by consequence, the installation condition degrades faster.
Summarizing, resorting to the support devices has to be understood as a provisional step until the grout properly placed is able to assume the function of precisely and permanently maintain the equipment in position; so that, chocks, wedges, shims, and similar are not acceptable as supporting system
5. What Phases Of The Project Does Apoltec Cover?
We work with critical machinery for our clients’ manufacturing processes, each machine is unique to us, and each problem is a challenge. We have more than 30 years diagnosing and solving foundation problems. Problems can originate both inside (mechanical problems) and outside the machinery (poorly distributed stresses, foundation cracks, etc.)
Apoltec is a turnkey engineering, we are specialists in covering the entire project from problem detection to engineering and execution. This is why we have a human team capable of moving quickly through the US, North Africa and Asia, as well as the latest technology in the sector.
6. What Type Of Machinery Do We Have Experience With?
We are specialists in dynamic equipment and on-site repairs machinery, but we have also carried out more than 400 repairs of static machinery. We have more than 30 years of experience repairing foundation problems, foundation consolidation through resin injection, regrouting, repair and replacement of anchor bolts, etc.
Apoltec is a turnkey engineering, we are specialists in covering the entire project from problem detection to engineering and execution. This is why we have a human team capable of moving quickly through the US, North Africa and Asia, as well as the latest technology in the sector.
7. Why Install With Epoxy Grout?
Our epoxy grout has many advantages over other grouts, such as cementitious ones, especially in aggressive and corrosive environments, where cement and concrete are not recommended. The main benefits compared to other grouts are:
- Greater resistance to compression and traction
- Waterproofing and crack sealing
- Higher hardness
- Better dissipation/transmission of vibrations to the ground providing greater stability.
8. Why Is It Important To Have These Repairs Done By A Foundation Specialist?
To combine mechanical requirements, equipment design and simple concrete forms is not an easy task. Pursuing to fit the equipment and ancillary design, concrete shapes become complicated, plenty of discontinuities through construction joints among blocks and plinths connection.
Sometimes, revamping means enlargement and form adaptation. Mass addition has to be continuous with the existing one taking care particularly on rebar connection and mass adhesion.
APOLTEC offers its experience and knowledge to our customers to simplify procedures and to adjust investment resources.
We work with and for the main heavy industry producers, and with critical machinery for their production system, for this reason each repair is carried out with the utmost detail and care, therefore we have a trained and professional human team, as well as the technological equipment necessary to carry out the project in record time and with excellent results.